工程展示
>>more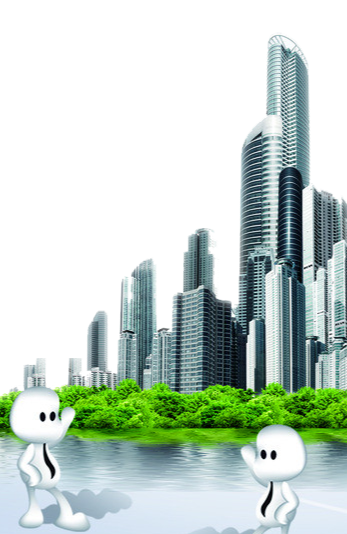
ABOUT
汕頭市節(jié)能環(huán)保科技有限公司創(chuàng)建于1998年,是一家專(zhuān)業(yè)致力于廢氣、污水、粉塵、噪聲治理,廠(chǎng)房節(jié)能降溫設(shè)備的研發(fā)、制造、工程設(shè)計(jì)和安裝的系統(tǒng)集成企業(yè)。多年來(lái)公司產(chǎn)品及系統(tǒng)工程設(shè)計(jì)能力,為各行業(yè),眾多企業(yè)提供了品質(zhì)高的環(huán)境治理及工業(yè)節(jié)能服務(wù)。產(chǎn)品經(jīng)國(guó)家電器檢測(cè)中心,質(zhì)量技術(shù)監(jiān)督局,疾控中心等部門(mén)測(cè)驗(yàn)合格,獲得五次技術(shù)專(zhuān)利;工程項(xiàng)目通過(guò)了國(guó)家環(huán)保檢驗(yàn)檢測(cè),受到用戶(hù)好評(píng)。
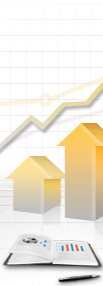
新聞資訊
>>more- 2020-1120
-
冷風(fēng)柜 風(fēng)幕柜 立風(fēng)柜有什么區(qū)別
冷風(fēng)柜和立風(fēng)柜是自風(fēng)幕柜的另一種名稱(chēng)。它的制冷原理是利用冷氣從背部吹出,讓冷氣均勻的覆蓋到風(fēng)幕柜的各個(gè)角落達(dá)到產(chǎn)品保鮮的效果。
- 2020-1021
-
污水處理的意義?
污水處理的意義:將污水進(jìn)行處理之后,可以對(duì)其進(jìn)行循環(huán)使用,為我國(guó)的生產(chǎn)減少水資源的消耗。水處理技術(shù)利用相關(guān)的技術(shù)手段對(duì)污水進(jìn)行凈化,使其可以繼續(xù)使用,所以污水處理很重要。